
All content presented here and elsewhere is solely intended for informational purposes only. The reader is required to seek professional counsel before beginning any legal or financial endeavor. |
So what exactly is equipment management software? Basically, it’s a specialty type of software system that business owners use to help them manage and track new or used equipment for their business. It improves efficiency, consistency, and maximizes the equipment’s lifespan. It also improves equipment-related safety and can potentially increase the equipment’s return on investment (ROI).
More About What Is Equipment Management Software
Equipment management software is a software system that is set up in one of two ways: as a services based software or as a mobile application. It’s designed to more efficiently, effectively, and safely manage whatever kind of new or used equipment and tools your company works with. It can be used to plan, schedule, and prioritize tasks.
It can also help increase the lifespan of your equipment and keep it on an orderly repair and maintenance schedule. It’s used by a multitude of different businesses around the world. Another function of the software is to help manage inventory. In fact, nearly $1.1 trillion of working capital is tied up in inventory. Imagine all the good those funds could do, if they were properly allocated. That’s one of the things inventory management software can help you with.
What Types of Companies Use Equipment Management Software?
Equipment management software can be useful to almost any business. Some businesses that use this type of software include:
- Maintenance companies
- Facilities management businesses
- Retail businesses with large numbers of inventory
- Warehouses
- Equipment rental companies
- Manufacturing companies
- Fleet maintenance
- Food, beverage, and hospitality companies
- Industrial cleaning companies
- Automotive industries
- Oil and gas companies
Popular Equipment Management Software Brands
Prices and features vary from vendor to vendor. Some of the most popular equipment software management brands and their pricing structures are as follows:
1. FMX: Pricing is based on the number of users, students enrolled (if it’s used for a school), features selected, and add-ons. The company will provide a custom quote for you.
2. Asset Panda: Various annual plans to fit your unique needs. Plans to help you manage 250 assets to over 5,000 assets.
4. Fleetio: Prices range from $3 to $7 per vehicle per month, if billed annually. If you have a fleet over 500 vehicles, you can request custom pricing.
5. Emaint: Prices range from $69 to $129 per user per month and each tier offers different features and capabilities
6. GoCodes: Pricing ranges from $500 to over $2,500 per year depending on the number of assets you need to track and manage.
7. Share My Toolbox: Pricing starts at $65 per month for one administrator and you can add on users for $50 each per month.
8. EZ OfficeInventory: Prices start at $35 per month to track 250 items with unlimited users. Higher-tiered plans and custom plans are available if you need to track more items.
9. MaintainX: The company offers a basic free subscription and if you need more features, pricing ranges from $8.33 per month to more than $32.50 per month per user.
10. Coast: Free options are offered as well as paid options with more features that range from $12 per user per month to $24 per user per month.
Cost Considerations of Implementing Equipment Management Software
The advantage, among many, of equipment management software is that it can help businesses save money by minimizing downtime due to preventative maintenance or troubleshooting, as well as offering data-driven insights into how to operate equipment more efficiently.
The cost varies greatly depending on the features selected, but in general it includes upfront setup fees for purchasing and integrating software solutions, ongoing subscription fees, personnel costs for implementation and training, hardware costs for installation, potential customization requirements, and additional implementation services.
Upfront Setup Fees: The costs of purchasing the software solution as well as any additional integration required.
Ongoing Subscription Costs: Expenses for continuing to use the system, which may include support or access to upgraded versions/features.
Human Costs: The cost of deploying the system, training users on how to use it appropriately, and making modifications as needed.
Hardware Costs: The costs of installing hardware components or devices required for system operation.
Extra Implementation Services: The cost of additional services required to properly install the system, such as project management or consulting.
Data Storage Costs: Extra charges for securely storing and preserving data created by the system.
Integration Fees: Charges for integrating equipment management software with current enterprise systems.
Regulatory Compliance Costs: The costs of adhering to government regulations or industry standards.
Examples of How Companies Can Use Equipment Management Software
Companies can detect the exact nature of any difficulties that may occur and take corrective action by tracking the performance of each piece of equipment over time. Equipment management software can also assist businesses in making educated selections when purchasing new assets or replacing old ones. Here are some examples of how businesses might use equipment management software:
Forecasting Maintenance Needs: Businesses may use the data produced by asset management software to effectively forecast when maintenance needs will develop and schedule accordingly to avoid unanticipated downtime.
Asset Tracking: Asset management software helps firms to measure how each asset is used over time, allowing them to make better resource allocation and utilization decisions.
Scheduling Replacements: By analyzing usage data, businesses may set up automated replacements for worn or obsolete assets before they affect service levels.
Cost Estimation: With the data collected in equipment management software, businesses can simply compute the overall cost associated with any specific asset.
Monitoring Performance Metrics: Businesses now have access to real-time performance metrics for every piece of equipment, allowing them to solve any issues that occur before they become major concerns.
Why Is Equipment Management Important?
Equipment management is a critical component of running a profitable business. It aids in ensuring that all necessary equipment is in good working order, safe, and accounted for. Effectively managing firm equipment also enables businesses to track spending and stay on top of maintenance and repairs. It also aids in increasing workplace efficiency and productivity while lowering overhead expenditures.
- Doing preventive maintenance: Preventative maintenance is evaluating equipment on a regular basis to identify potential problems before they occur, so preventing costly repairs or replacements later on.
- Asset tracking: This enables you to track the use and performance of your assets over time, allowing you to make more informed decisions about when to replace them or budget for repairs and upgrades.
- Improving inventory control: Understanding what supplies you'll need ahead of time cuts waste and wasteful spending while also allowing you to fulfill deadlines more efficiently.
- Process automation: Process automation can save time by removing manual data entry or repetitive operations; it also decreases errors caused by human input errors.
- Quickly identifying breakdowns: By frequently monitoring your equipment, any issues can be recognized early on, allowing corrective actions to be conducted without disruption caused by downtime or lost productivity from machinery outages.
- Lowering energy consumption: Correctly maintained equipment consumes less energy, resulting in cheaper power bills for the organization and a better environment overall.
- Improving safety measures: Being up to date on safety protocols ensures that staff are following proper safety protocols, which may prevent costly lawsuits resulting from damage caused by negligence on the part of the company's management team.
- Labor cost monitoring: Equipment management makes it easier to keep track of how much labor is being used at any given time; this information can then be used to optimize staffing levels based on the needs of the business at the time, resulting in increased profitability over time due to lower labor expenses compared to production output.
Common Features of Equipment Management Software
There are certain features that you will find in most equipment management software, but keep in mind that some features differ from vendor to vendor and will depend on the level of service you choose, how many users you use, and how many assets you need to manage.
Some popular software features include:
Asset Tracking
Asset tracking is the method by which you keep track of your assets, inventory, or equipment. You may track it with bar codes, use GPS tags to monitor movement, or radio frequency identification to broadcast its location. Bluetooth systems, serial numbers, batches, and electronic recording are also used to track assets. You want to know where your asset is at all times and you can do that with asset tracking and management features.
For example, you own a fleet of trucks that are dispersed throughout the country. Each truck will have its own GPS and the software will allow you to check where the truck is, how many miles it has driven, and when it reaches its final destination. You can keep track of mileage, unauthorized stops, and keep your timeline on track.
Work Orders Management
This feature allows you to create, complete, and analyze work orders quickly and efficiently. Some software can be used on any device so you can manage work orders from your smartphone, laptop, or your tablet. By managing your work orders in a timely fashion, you’re increasing productivity, minimizing asset downtime, and boosting asset performance.
If you’re in charge of a maintenance company, you may need to keep track of hundreds of work orders each day. It’s much easier to use software to help you do that, than remembering to write everything down by hand.
Preventative Maintenance
Performing preventative maintenance on any piece of equipment or vehicle, extends its useful life, and decreases the chances that it will break down or cause an accident. This feature streamlines and simplifies the process with checklists and reminders. You can see what types of preventative maintenance has already been done on each asset, when its next service is due, and if anything is overdue.
Predictive Maintenance
This feature is similar to preventative maintenance but it actually ‘predicts’ if and when the equipment will have an issue before it happens. It’s able to do this by monitoring equipment usage, condition, and performance overtime. Its goal is to predict the problem, alert the operator, and fix it before it causes any issues.
Inventory Management
Inventory management is challenging for most businesses large and small. These features help businesses track inventory levels, sort them, keep track of orders, deliveries, and sales, and store them in one organized, up-to-date, easily-accessible place. You can automate processes which aids in reducing costs. You can scan barcodes, analyze trends, predict shortages, increase ordering, and keep optimal levels of inventory on hand.
This is especially helpful for businesses who have fluctuating levels of inventory and may have peak seasons. Using an inventory management feature can help ensure you don’t run out of product during your busy season and you don’t order too many products during slower periods.
Labor Resource Management
Labor is what keeps your company running. They’re quite literally the most important part of your company and you want to make sure that they are performing as optimally as possible. Use this labor resource management feature to manage the number of hours worked, overtime, payroll budgets, schedules, time off, and team productivity.
You can also plan for how long work orders should take based on previous similar jobs. Plan the number of technicians needed on a particular project so you don’t have too few or too many technicians on staff.
Equipment Planning
The type of equipment planning you need to do will depend on the type of equipment your business requires. For example, a medical facility will have more inspections and quality control on their equipment than a warehouse may have.
Equipment planning features help you budget for new equipment, schedule inspections, check on delivery times, and delivery schedules, and analyze the layout and storage of the equipment before it arrives. It may also help configure new networks and security requirements.
Reporting
You want to be able to keep track of your numbers and have them reported in real time, regardless of what industry you’re in. Knowing your numbers can be the difference between running a successful business and one that is on the brink of failure.
This feature will turn raw data into powerful insights that you can analyze to make the best decisions for your company. You can access the dashboard and check out daily reports, compare year-over-year data, and check out trends and compare it to overall industry data. You can print out diagrams, import data, export reports, and share them with other employees and clients.
Vendor Management
Rather than using different software or systems for each vendor, you can manage all of your vendors in one place. This cuts down on time and increases accuracy. You can store vendor information in a place that is safe, secure, and easily accessible for authorized users. You can also review vendor’s past performances and decide if you want to use them again or would be better off with a different company. Vendor management can also be used alongside work orders and inventory tracking features. Additionally, you can keep track of billable hours for someone that may work for you a few times a year.
Benefits of Equipment Management Software
Companies can enjoy numerous benefits when implementing equipment management software.
Improve Asset Reliability
By monitoring your asset, using it as intended, and using preventative and predictive maintenance features, you can improve the reliability of your asset. Basically, if you know where your asset is, what it’s doing, and when it should be serviced, you can increase its reliability.
Minimize Unplanned Downtime
Track your assets so you don’t have unplanned downtime. By using equipment management software, you’re using the equipment as much as it can be used, so you’re not wasting time or money. You’re able to track its movements and reduce underutilization. There’s no point in spending thousands of dollars on a piece of machinery if you forget to use it or are only using it sporadically.
Cut Back on Waste and Spoilage
This is especially applicable in the food, beverage, and retail industries. If you’re tracking inventory, you won’t order more than you need and will reduce or eliminate waste or expired goods. This also reduces having to sell extra inventory off at low prices because you have no room for it or because it’s about to hit its expiration date.
Decrease Work Order Resolution Times
Software can help you optimize work order timeliness and respond more efficiently to work orders. You can create work order benchmarks for all team members to see, so they know approximately how long a work order should take. By automating much of the work order process, you’re able to get the work order input, assigned, finished, and followed up on much quicker than without using an equipment management system.
Reduce Maintenance Costs
By using the maintenance related features in your equipment management software, you can keep track of maintenance schedules, follow the guidelines of how and when to use the equipment, check out service records, and use the software to track the costs instead of allocating additional resources to labor for that purpose.
Extend Asset Lifespan
An asset’s lifespan can be extended when it is used properly, stored properly, and when preventive maintenance is performed. It’s also extended when necessary repairs are completed in a timely manner. All of this can be tracked and allocated in the equipment management app. By extending an asset’s lifespan, you save money because you don’t need to purchase a new piece of equipment as soon.
Maintain Safety and Compliance Regulations
All industries have some sort of safety and compliance regulations. Whether you’re in the medical field, food and beverage, construction, or manufacturing, you need to follow the rules and regulations to ensure the safety of your employees, your products, and your consumers.
Equipment management software can alert you to upcoming inspections, store safety regulations in a secure but easily accessible space, and keep track of any violations or safety incidents.
Reduce Risk and Liability
To reduce risk and liability, make sure that equipment operators are properly trained on the equipment they’re going to use. You can store training manuals, information booklets, and other pertinent information in your equipment management software. You can also customize the software so you can see who is up to date on necessary certifications and licenses, thus reducing your risk and overall liability.
Improve Capital Planning
New equipment can be expensive and you want to see where the capital is coming from to purchase it. Check out one of the spreadsheets or data graphs in your software or app to see how much you have to allocate towards a new piece of equipment and when the best time to purchase it is. You can also see previous trends on capital planning and usage and learn from any past mistakes.
How to Choose Equipment Management Software
When choosing equipment management software, consider how you’re going to use the software, what functions you need, what integrations you require, what your budget is, and how many people will be using the software. Also, consider the following when choosing the best software for your business:
What Kind of Buyer Are You?
There are three main types of buyers; decide which one most accurately describes yourself:
- Full Suite Buyer: This type of buyer typically has a large or unlimited budget, may be part of a large company, or manage an extensive amount of assets. They want the ‘full suite’ of products and features. The top tier plan or a custom plan with all the bells and whistles is what you want. You want software to be automated, seamless, have dozens of functions, and integrations, and have a team of dedicated support to teach you or your staff how to use it.
- Specialty Buyer: You want software that fulfills a specific need. You may be looking for a very specific function such as inventory management or real-time asset tracking from a mobile device. You don’t necessarily need something with all the features; you just want to make sure it has exactly what you need.
- Small Business Buyer: You are a small business who doesn’t necessarily have a lot of capital to invest in software but you realize it's advantages and want to give it a try. You may only need a platform for one or two users and you will take advantage of a demo or a free trial version of the software to see if it’s a good fit. You don’t want software that has a minimum number of required assets or that’s specifically designed for a larger company.
Types of Equipment Management Software
Typically, there are two different delivery methods for equipment management software:
- Mobile Applications: This software can be used from any smartphone, tablet, or computer. It can be used on the go and is convenient if you want to be able to manage your equipment from wherever you are.
- Software as a Service (Saas): This is a licensing and delivery model of software that is centrally hosted. It can be web based or you may need to physically download it. It may not be mobile-compatible and may have more features than mobile applications but doesn’t have the flexibility.
What to Look for in Equipment Management Software
It’s important to look for the following factors in equipment management software:
Customer service: Is it included, when are they available, and how can you reach them?
- Company reviews: What’s the overarching trend? What do users like and dislike
- Company reputation: How long has it been around? Is it reputable? You don’t want a fly by the night software company that takes your money and then disappears
- Integrations: What other software or apps is it compatible with? What is not compatible with it?
- Features: Check out each of the features and make sure you’re going to use what you pay for.
- Demo or free trial: Can you test the software before you buy it?
- Industries: Is your industry mentioned as one of the ones they work with? If not, ask if they have software tailored to your industry. You don’t want to end up purchasing software for a fleet business if you are a manufacturer.
Equipment Management Software to Harness Real-Time Data and Make Smarter Decisions Quickly
Equipment management software is a strong tool that can help businesses of all sizes stay organized. This type of software enables businesses to use real-time data to make better decisions more rapidly. Businesses may get an up-to-date view of all their assets and operations by employing equipment management software. Businesses have access to precise equipment information such as maintenance records, asset performance data, and consumption trends.
This information allows them to anticipate possible problems with their equipment and arrange for maintenance or repairs. Furthermore, this software allows firms to track the performance of each individual piece of equipment in order to optimize operations and discover areas for development.
These are seven practical ways that Asset Management Software can assist businesses in harnessing real-time data:
Automated Reports: Users can generate automated reports that provide a full overview of assets in real-time with high accuracy. These reports are completely configurable and can be scheduled automatically based on the user's choices.
Predictive Maintenance: Predictive maintenance employs predictive algorithms in conjunction with asset performance data collected from the system to detect potential issues before they occur, allowing businesses to proactively address any issues that arise with their equipment before it fails completely or disrupts operations.
Asset Tracking: Asset tracking software makes it easier for businesses to keep track of multiple pieces of equipment within an organization by providing detailed information about each asset's performance over time, as well as other relevant details such as its location or condition at any given time, so that necessary actions can be taken quickly and efficiently, without any disruption caused by delays or confusion caused by manual tracking methods.
Real-Time Alerts: Real-time alerts notify users when certain actions occur that are directly or indirectly related to a specific piece of business's assets, such as when an issue arises that requires attention or when new updates for the respective asset are made available, among other things, giving users more control over how they manage their assets without having to constantly monitor them manually.
Workflow Optimization: The workflow optimization tool enables users to examine complete processes in order to better understand how different components interact inside an organization's systems, allowing them to make smarter decisions faster.
Data Visualization: Data visualization tools allow users to easily gain insights from complex datasets through visually appealing charts, graphs, heatmaps, and so on, which not only saves time but also allows decision makers to interpret results faster than ever before, resulting in more informed decisions being made faster than ever before.
Integration: Integration capabilities enable organizations to integrate third-party applications into existing systems, making it easier for organizations to extend existing features offered by the tool while providing seamless integration between two previously disparate systems, resulting in improved productivity as well as cost savings due to a reduction in manual processes that would otherwise necessitate extensive resources.
Equipment Management Software to Enhance Collaboration Between Employees, Vendors, and Customers
Equipment management software provides a platform for all stakeholders to access the same information in real time, allowing them to make quick and precise judgments. This type of software also enables employees, vendors, and consumers to collaborate on projects or tasks more effectively by fostering communication and organization. It reduces the need for many apps or systems because all data may be saved in a single location.
Businesses can streamline procedures such as procuring supplies or services, tracking progress in projects or tasks, negotiating terms with vendors more effectively, and delivering better customer service through streamlining communications. Here are seven ways that asset management software can improve communication among employees, vendors, and customers:
- Process Automation: Automates repetitive operations such as ordering supplies to save time while enhancing order accuracy.
- Convenient Access: Allows users to quickly access critical information from any device with an internet connection, increasing productivity.
- Streamlined Collaboration: Enables users from different locations or departments to collaborate on tasks more efficiently by storing all relevant data in a single system rather than several systems.
- Event Logging & Auditing: Enables users to quickly monitor events connected to their actions for auditing purposes, simplifying compliance.
- Increased Communication: Allows for timely updates between users, which aids in the improvement of customer service quality.
- Advanced Security Features: Provides advanced security features such as role-based permissions, ensuring that only authorized personnel have access.
- Tailored Reports & Analytics: Creates insightful reports that enable managers to make better decisions based on data collected.
Monitor Customer Satisfaction Easily Through Analysis Provided by Equipment Management Software
Customer happiness is a critical component of every successful organization. Customer feedback may be easily viewed and analyzed in real time thanks to equipment management software. The program enables organizations to respond promptly to client feedback, enhancing customer experience and loyalty. Companies can use this software to identify areas where their services or goods fall short, allowing them to improve their offerings and remain competitive in the market.
Monitor Customer Service Performance: This feature enables businesses to monitor important performance indicators such as response times, resolution rates, and overall customer service performance. This assists in identifying areas for service improvement and boosts client happiness over time.
Evaluate Consumer Sentiment: By evaluating replies from surveys, emails, and other data sources, organizations can understand how customers feel about a product or service. This allows businesses to swiftly determine which components of their products or services are popular with clients and which need to be improved. Sentiment analysis provides businesses with significant insight into how customers truly feel about a product or service by examining verbatim replies from surveys and other sources of data.)
Monitor Feedback Channels: Equipment management software enables organizations to monitor a variety of feedback channels, including social media, email campaigns, and others, in order to obtain a better knowledge of what people are saying about them online.
Personalize Reports and Dashboards: Customized reports enable users to build tailored reports based on specified criteria, allowing them to conveniently track results over time.
Automate Tasks & Alerts: The software's automation features allow users to set up actions that run automatically at pre-defined periods or when triggered by specific situations. This allows users to stay up to date without having to actively check for updates.
Interact with Customers Easily: Communication options included into the program make it easier for businesses to contact with customers via emails, SMS messages, and other means, simplifying the process for both parties.
Quickly generate extensive reports: With automated reporting capabilities, users may quickly generate accurate information such as trends, comparisons, and so on, assisting in the identification of patterns that may be beneficial in the future.
Gaining Insights Into Risk Factors Quickly from Equipment Management Software
Getting immediate insights into risk factors through equipment management software can offer a company with the information it needs to make informed decisions and boost safety. Business managers can use this software to review and analyze data about their operations, such as maintenance plans, equipment utilization rates, and other performance metrics.
This enables them to discover possible risks in their operations before they become too significant or costly to mitigate. Furthermore, the software can provide proactive measures to ensure safe operations. Businesses that provide real-time data analysis and reporting capabilities can detect patterns or flaws in their operations earlier than if they relied on manual methods.
- Maintenance Plans: Users of equipment management software can create detailed maintenance plans for their assets based on specific needs and requirements. This ensures that assets are properly cared for and that any potential issues are addressed before they become larger issues.
- Equipment Utilization Rates: Software is designed to monitor equipment utilization rates across all business locations so managers can gain a better understanding of how much each asset is used over time and determine if additional resources are required for optimal performance.
- Real-Time Data Analysis: Businesses will have access to real-time information about their operations thanks to advanced analytics tools integrated into the software, allowing them to make better decisions faster when it comes to reducing risk factors associated with their equipment management process.
- Proactive Measures: The proactive features available in this type of software allow users to plan ahead by setting up preventive maintenance tasks or alerts when certain thresholds on an asset's performance levels or usage patterns have been reached, which helps keep overall operating costs down by catching issues early before they become more expensive problems later on.
- Asset Tracking & Inventory Management: The tracking features built into these systems allow businesses to track all of their assets in one place, including serial numbers, model/make numbers, and location details, making it easier to keep track of where all company owned assets are at any given time, even if those same items move around between different locations frequently throughout the month or year, allowing for accurate inventory control over those same items.
- Reporting Capabilities: The reporting capabilities provided by this type of system enable managers to obtain a comprehensive overview of any issue directly related to a specific asset, such as repair history, downtime statistics, and so on, making it easier for decision makers to identify any underlying trends within their operation that may require further investigation in order to gain additional insights quickly from available data sets generated automatically via system.
- Automated Workflows & Alerts: Users can set up automated workflows triggered by certain events, such as maintenance schedules being completed, so they don't have to manually check every item on the list every single day, while also receiving notifications whenever certain thresholds, such as low inventory levels, have been reached, so that corrective actions can be taken immediately without having to wait until the issue becomes a bigger problem later down the line due to lack of foresight from inaction.
Final Word
Equipment management software helps you manage different kinds of equipment in a variety of capacities. It can help you track inventory, manage reports, track moving assets, and manage labor. The software is intended to help businesses more efficiently and effectively mange their assets.
Now that you know how to manage equipment of your business efficiently, you might be interested in beneficial ways of increasing your equipment budget. Take a look at our list of the best equipment financing companies to learn more about funding opportunities they have to offer.
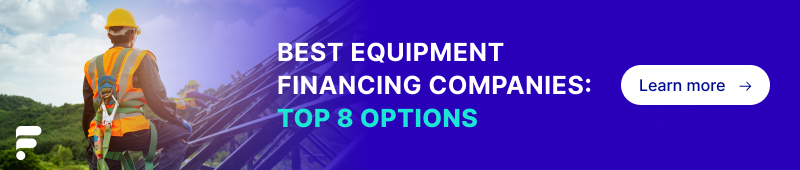